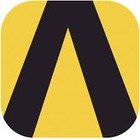
Description: ANSYS Workbench is engineering simulation software used for finite element analysis. It has a wide range of applications in structural, thermal, fluid, and electromagnetic simulations across industries like aerospace, automotive, energy, and electronics.
Type: Open Source Test Automation Framework
Founded: 2011
Primary Use: Mobile app testing automation
Supported Platforms: iOS, Android, Windows

Description: Impact Finite Element is finite element analysis software used to simulate high-velocity dynamic events like crashes, impacts, and explosions. It can analyze the effects of these events on structures and components.
Type: Cloud-based Test Automation Platform
Founded: 2015
Primary Use: Web, mobile, and API testing
Supported Platforms: Web, iOS, Android, API