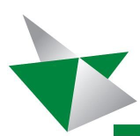
Description: Siemens Teamcenter is a Product Lifecycle Management (PLM) software suite that helps companies manage the entire lifecycle of products from conception and design to manufacturing, support and end of life. It provides product data management, CAD integration, bill of materials management, and more.
Type: Open Source Test Automation Framework
Founded: 2011
Primary Use: Mobile app testing automation
Supported Platforms: iOS, Android, Windows
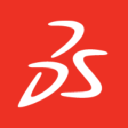
Description: SolidWorks PDM is product data management software designed for engineers and designers to manage, track, and collaborate on CAD file data. It integrates with SolidWorks to provide version control, search, automation, workflow, and other features.
Type: Cloud-based Test Automation Platform
Founded: 2015
Primary Use: Web, mobile, and API testing
Supported Platforms: Web, iOS, Android, API