
Description: GoNest 2D is a 2D nesting software used for optimizing material usage and reducing waste in manufacturing. It allows you to efficiently nest irregular 2D parts onto stock sheets. The software is easy to use with drag and drop functionality.
Type: Open Source Test Automation Framework
Founded: 2011
Primary Use: Mobile app testing automation
Supported Platforms: iOS, Android, Windows
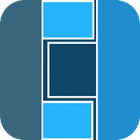
Description: iOptiCut is an optimization and nesting software for the sheet metal and fabrication industry. It helps reduce material waste and costs by efficiently nesting parts on stock sheets. The software analyzes part shapes and determines the optimal layout to maximize material usage.
Type: Cloud-based Test Automation Platform
Founded: 2015
Primary Use: Web, mobile, and API testing
Supported Platforms: Web, iOS, Android, API